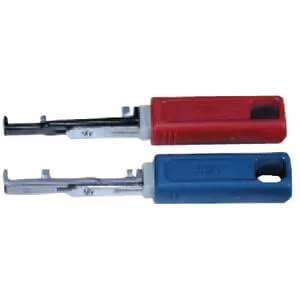
The term “TG tube” refers to a crucial component used across various industries, particularly in heat transfer and mechanical systems. These tubes are designed to perform under extreme conditions, providing efficiency and durability. If you’ve ever come across a TG tube and wondered what it is or how it functions, you’ve come to the right place. In this article, we’ll explore the purpose of TG tubes, the materials used to manufacture them, and their applications in different sectors.
We’ll also take a closer look at the various types of TG tubes and how they differ, providing you with an in-depth understanding of this versatile tool. Whether you’re in engineering, construction, or manufacturing, knowing about TG tubes is essential for optimizing performance in your projects. So, let’s dive into the world of TG tubes and discover everything you need to know.
What is a TG Tube?
A TG tube is a type of tubular component often made from metals such as stainless steel, copper, or aluminum. These tubes are typically used in heat transfer systems, as their design allows for efficient conduction of heat or fluid flow. TG tubes come in various sizes, depending on their intended use, and can be tailored to meet the specific needs of different industries.
TG tubes are essential in settings where high temperatures or pressures are involved. Their main function is to transport fluids or gases while maintaining structural integrity under extreme conditions. Whether it’s in a refrigeration system, automotive engines, or large-scale industrial applications, TG tubes are vital to the operation of many systems.
TG Tube: Everything You Need to Know
The term “TG tube” refers to a crucial component used across various industries, particularly in heat transfer and mechanical systems. These tubes are designed to perform under extreme conditions, providing efficiency and durability. If you’ve ever come across a TG tube and wondered what it is or how it functions, you’ve come to the right place. In this article, we’ll explore the purpose of TG tubes, the materials used to manufacture them, and their applications in different sectors.
We’ll also take a closer look at the various types of TG tubes and how they differ, providing you with an in-depth understanding of this versatile tool. Whether you’re in engineering, construction, or manufacturing, knowing about TG tubes is essential for optimizing performance in your projects. So, let’s dive into the world of TG tubes and discover everything you need to know.
What is a TG Tube?
A TG tube is a type of tubular component often made from metals such as stainless steel, copper, or aluminum. These tubes are typically used in heat transfer systems, as their design allows for efficient conduction of heat or fluid flow. TG tubes come in various sizes, depending on their intended use, and can be tailored to meet the specific needs of different industries.
TG tubes are essential in settings where high temperatures or pressures are involved. Their main function is to transport fluids or gases while maintaining structural integrity under extreme conditions. Whether it’s in a refrigeration system, automotive engines, or large-scale industrial applications, TG tubes are vital to the operation of many systems.
Types of TG Tubes
Standard TG Tubes
Standard TG tubes are the most common type and are often used in everyday applications, such as plumbing, refrigeration, and air conditioning systems. They are typically made from durable materials like stainless steel or copper and are known for their reliability in medium to high-pressure environments.
High-Pressure TG Tubes
High-pressure TG tubes are specifically designed for environments where the pressure is significantly greater than normal. These tubes are reinforced with thicker walls and stronger materials, allowing them to withstand the high demands of industries like oil and gas, as well as chemical processing plants.
Heat Exchanger TG Tubes
Heat exchanger TG tubes are specially designed for optimal heat transfer. These tubes are commonly used in boilers, condensers, and evaporators. The primary goal is to efficiently transfer heat from one fluid to another without mixing the two, making them vital in thermal power plants and air conditioning systems.
Corrugated TG Tubes
Corrugated TG tubes have a ridged design that allows for greater flexibility and thermal expansion. These are ideal for situations where the tube needs to move or expand, such as in steam systems or certain types of reactors. Their flexible nature makes them highly adaptable to changing environmental conditions.
Custom TG Tubes
Custom TG tubes are tailored to specific requirements, offering unique dimensions, materials, or coatings depending on the application’s needs. These are often used in specialized equipment, where the standard tube may not meet the performance criteria. Custom tubes are common in niche industries such as aerospace and advanced manufacturing.
Materials Used in TG Tubes
Stainless Steel
Stainless steel TG tubes are widely used because of their resistance to corrosion, high temperature tolerance, and overall strength. They are suitable for a variety of applications, including those in food processing, pharmaceuticals, and chemical industries.
Copper
Copper TG tubes are excellent conductors of heat and electricity, making them ideal for heat exchangers, refrigeration systems, and electrical wiring. They are also resistant to corrosion, although they may not handle extreme pressure as well as stainless steel.
Aluminum
Aluminum TG tubes are lightweight and offer good thermal conductivity. They are commonly used in automotive and aerospace industries due to their ability to provide efficient cooling in light-weighted applications.
Nickel Alloys
Nickel alloys are known for their high corrosion resistance and ability to perform under extreme temperatures. These TG tubes are usually found in highly specialized industries such as nuclear power plants or deep-sea exploration.
Applications of TG Tubes
HVAC Systems
One of the most common uses for TG tubes is in heating, ventilation, and air conditioning (HVAC) systems. These tubes help transport refrigerants and air between different components, ensuring that the system maintains the desired temperature.
Industrial Manufacturing
In industrial settings, TG tubes are often used to transport liquids or gases under high pressure or temperature. Whether it’s in a factory, refinery, or chemical processing plant, these tubes play an essential role in maintaining smooth operations.
Automotive Industry
TG tubes are integral to the automotive industry, especially in the construction of cooling systems for engines. The tubes help dissipate heat from the engine, ensuring optimal performance and preventing overheating.
Power Plants
Power plants rely heavily on heat exchanger TG tubes to transfer thermal energy from steam or other fluids. These tubes must be incredibly durable and efficient to handle the extreme heat and pressure found in such environments.
Medical Equipment
In the medical field, TG tubes are used in various devices and systems, such as those for sterilization or fluid transfer. The precision and safety required in these applications mean that the quality of TG tubes is of utmost importance.
Advantages of Using TG Tubes
Durability
One of the main benefits of using TG tubes is their durability. These tubes are built to withstand extreme conditions, such as high pressures, corrosive environments, and intense heat.
Versatility
TG tubes can be used in a wide range of industries, from automotive and aerospace to chemical plants and power generation. Their adaptability makes them a preferred choice for engineers and designers alike.
Cost-Effectiveness
While the initial investment in TG tubes may be higher than in less durable alternatives, their long lifespan and reduced maintenance costs make them a cost-effective option in the long run.
Efficiency
Especially when it comes to heat transfer, TG tubes are incredibly efficient. Their ability to quickly and effectively conduct heat makes them essential in systems where energy efficiency is key.
Common Issues with TG Tubes
Corrosion
Corrosion is one of the most common problems associated with TG tubes, particularly those made from metals like copper or stainless steel. Over time, exposure to certain chemicals or environmental conditions can cause the tube to degrade, affecting performance.
Pressure Cracks
In high-pressure applications, TG tubes can sometimes develop cracks due to the intense force being exerted on them. Regular maintenance and the use of high-quality materials can mitigate this risk.
Leakage
Leakage is another issue that can arise, particularly in older or poorly maintained TG tubes. It’s crucial to regularly inspect the tubes for signs of wear and tear to avoid costly repairs.
How to Maintain TG Tubes
Regular Inspections
One of the best ways to ensure your TG tubes remain in top condition is to conduct regular inspections. Look for signs of corrosion, leaks, or damage, and address these issues immediately.
Cleaning
Keeping TG tubes clean is essential, especially in systems where the tube is used to transport fluids or gases. Any buildup of dirt or debris can impede performance and lead to system failure.
Proper Installation
Ensuring that your TG tubes are installed correctly is key to their long-term performance. Poor installation can lead to leaks, cracks, or other issues that may require costly repairs.
How to Choose the Right TG Tube for Your Needs
Understand Your Application
Before selecting a TG tube, it’s important to understand the specific needs of your application. Are you dealing with high temperatures? High pressure? Corrosive substances? These factors will determine the best material and type of tube for the job.
Consider the Material
The material of the TG tube is crucial, as it will affect the tube’s performance under different conditions. Stainless steel is ideal for high-pressure situations, while copper is excellent for heat conduction.
Consult with Experts
If you’re unsure about which TG tube is right for your needs, it’s always a good idea to consult with a professional. Engineers and manufacturers can provide guidance on the best options for your specific requirements.
Conclusion
In summary, TG tubes are an essential component in various industries, offering durability, efficiency, and versatility. Whether used in HVAC systems, automotive cooling, or industrial manufacturing, TG tubes play a vital role in ensuring smooth operations. Understanding the types, materials, and applications of TG tubes allows you to make informed decisions when selecting the right tube for your needs.
By maintaining and regularly inspecting your TG tubes, you can ensure their long-term performance and avoid common issues like corrosion or pressure cracks. As we have seen, choosing the right tube for your application is key to optimizing performance and efficiency in your system.
FAQs About TG Tubes
What are TG tubes used for?
TG tubes are used in a variety of applications, including heat exchangers, HVAC systems, and industrial manufacturing. They transport fluids or gases while withstanding high temperatures and pressures.
How do I maintain a TG tube?
Regular inspections, proper cleaning, and ensuring correct installation are key to maintaining the longevity and performance of a TG tube.
What materials are TG tubes made from?
TG tubes are commonly made from stainless steel, copper, aluminum, or nickel alloys, depending on the application.
Can TG tubes withstand high pressure?
Yes, high-pressure TG tubes are specifically designed to handle intense pressure and are reinforced with thicker walls and stronger materials.
Are custom TG tubes available?
Yes, custom TG tubes can be manufactured to meet specific requirements, such as unique dimensions, materials, or coatings.